Ferrite magnets, also known as ceramic magnets, are a type of permanent magnet made from a chemical compound containing ceramic materials and iron oxide. They are known for their affordability, durability, and resistance to demagnetization, making them a popular choice for a wide range of applications.
Directory Listing:
What is a Ferrite Magents?
The ferrite is a new type of non-metallic magnetic material developed in the 1940s. It is a metal oxide with ferrimagnetism. In terms of electrical characteristics, the resistivity of ferrite is much larger than that of a single metal or alloy magnetic material, and it also has higher dielectric properties. The magnetic properties of ferrite are also manifested in high magnetic permeability at high frequencies. Therefore, ferrite has become a widely used non-metallic magnetic material in the field of high-frequency weak current. Due to the low magnetic energy stored in the unit volume of ferrite, the saturation magnetic induction (Bs) is also low (usually only 1/3 to 1/5 of pure iron), which limits its application in the field of low-frequency strong electricity and high power requiring higher magnetic energy density.
Composition and Manufacturing
The manufacturing process begins with accurately measuring and blending these raw materials to create a homogeneous mixture. This mixture is then finely ground to ensure uniform particle size, which is crucial for the consistency and quality of the final magnets.
The finely ground powder is then pressed into the desired shape using high-pressure molds. This pressing process compacts the powder into a "green body," a term used to describe the formed but unsintered magnet.
The green bodies are then subjected to a sintering process, where they are heated to temperatures between 1,000 and 1,300 degrees Celsius in a controlled atmosphere.
After sintering, the magnets are cooled and then undergo a magnetization process. In this step, the magnets are exposed to a strong magnetic field, which aligns the magnetic domains within the material, imparting permanent magnetism. The strength and orientation of the applied magnetic field are carefully controlled to achieve the specific magnetic characteristics required for the final product.
Types of Ferrite Magents:
-
Hard Ferrites: In contrast, permanent ferrite magnets are made of hard ferrites, which have a high coercivity and high remanence after magnetization. Iron oxide and barium carbonate or strontium carbonate are used in manufacturing of hard ferrite magnets. The high coercivity means the materials are very resistant to becoming demagnetized, an essential characteristic for a permanent magnet. They also have high magnetic permeability. These so-called ceramic magnets are cheap, and are widely used in household products such as refrigerator magnets.
- Soft Ferrites: Ferrites that are used in transformer or electromagnetic cores contain nickel, zinc, and/or manganese compounds. Soft ferrites are not suitable to make permanent magnets. They have high magnetic permeability so they conduct magnetic fields and are attracted to magnets, but when the external magnetic field is removed, the remanent magnetization does not tend to persist. This is due to their low coercivity. The low coercivity also means the material's magnetization can easily reverse direction without dissipating much energy (hysteresis losses), while the material's high resistivity prevents eddy currents in the core, another source of energy loss. Because of their comparatively low core losses at high frequencies, they are extensively used in the cores of RF transformers and inductors in applications such as switched-mode power supplies and loopstick antennas used in AM radios.
Key Characteristics:
One of their most notable features is their moderate magnetic strength, which, while not as powerful as neodymium magnets, is sufficient for many applications. This makes them particularly useful in devices where extreme magnetic force is not required. Another important characteristic is their excellent resistance to demagnetization, meaning they can maintain their magnetic properties even when subjected to external magnetic fields. This stability is critical for long-term use in various industrial and consumer products.
Temperature resistance is another significant advantage of ferrite magnets. They can operate effectively at high temperatures, typically up to 250 degrees Celsius, without losing their magnetic properties. This makes them suitable for applications in environments where other types of magnets might fail. Additionally, ferrite magnets are naturally resistant to corrosion. Unlike neodymium magnets, which often require protective coatings, ferrite magnets can withstand exposure to moisture and chemicals without degrading. This intrinsic corrosion resistance makes them ideal for outdoor and marine applications.
Cost-effectiveness is a key characteristic that sets ferrite magnets apart from other types of magnets. The raw materials used in their production, primarily iron oxide, are abundant and inexpensive, making ferrite magnets a cost-effective solution for a wide range of applications. Their manufacturing process is also relatively simple and low-cost, further contributing to their affordability.
Durability is another notable feature of ferrite magnets. They are hard and brittle, which makes them less prone to mechanical wear over time. However, this brittleness also means they need to be handled carefully to avoid cracking or chipping. Despite this, their overall durability and robustness make them suitable for many demanding applications. These key characteristics—moderate magnetic strength, resistance to demagnetization and corrosion, high-temperature performance, cost-effectiveness, and durability—make ferrite magnets a versatile and reliable choice for numerous industrial, commercial, and consumer applications.
Common Applications:
One of their most common uses is in electric motors, where their moderate magnetic strength and stability are essential for efficient performance. They are particularly prevalent in automotive applications, powering everything from windshield wipers to starter motors.
In the audio industry, ferrite magnets are a staple in the production of loudspeakers. Their ability to convert electrical energy into sound makes them ideal for this purpose, ensuring clear and consistent audio output. Similarly, they are used in microphones, providing the necessary magnetic field to capture sound accurately.
Ferrite magnets also play a crucial role in magnetic separators, which are used to remove magnetic materials from non-magnetic ones. This application is vital in industries like recycling and mining, where separating different types of materials efficiently is essential for operational success.
In the realm of consumer electronics, ferrite magnets are found in various devices, including televisions and computer monitors. They are used in deflection yokes, which help control the direction of the electron beam in cathode-ray tubes. Although this technology is becoming less common with the rise of LCD and LED screens, it still highlights the versatility of ferrite magnets.
Moreover, ferrite magnets are used in magnetic assemblies for holding, lifting, and separating tasks. Their strength and stability make them suitable for these applications, where reliable performance is critical. In sensors and meters, ferrite magnets help measure various parameters, from speed to position, providing accurate and dependable readings.
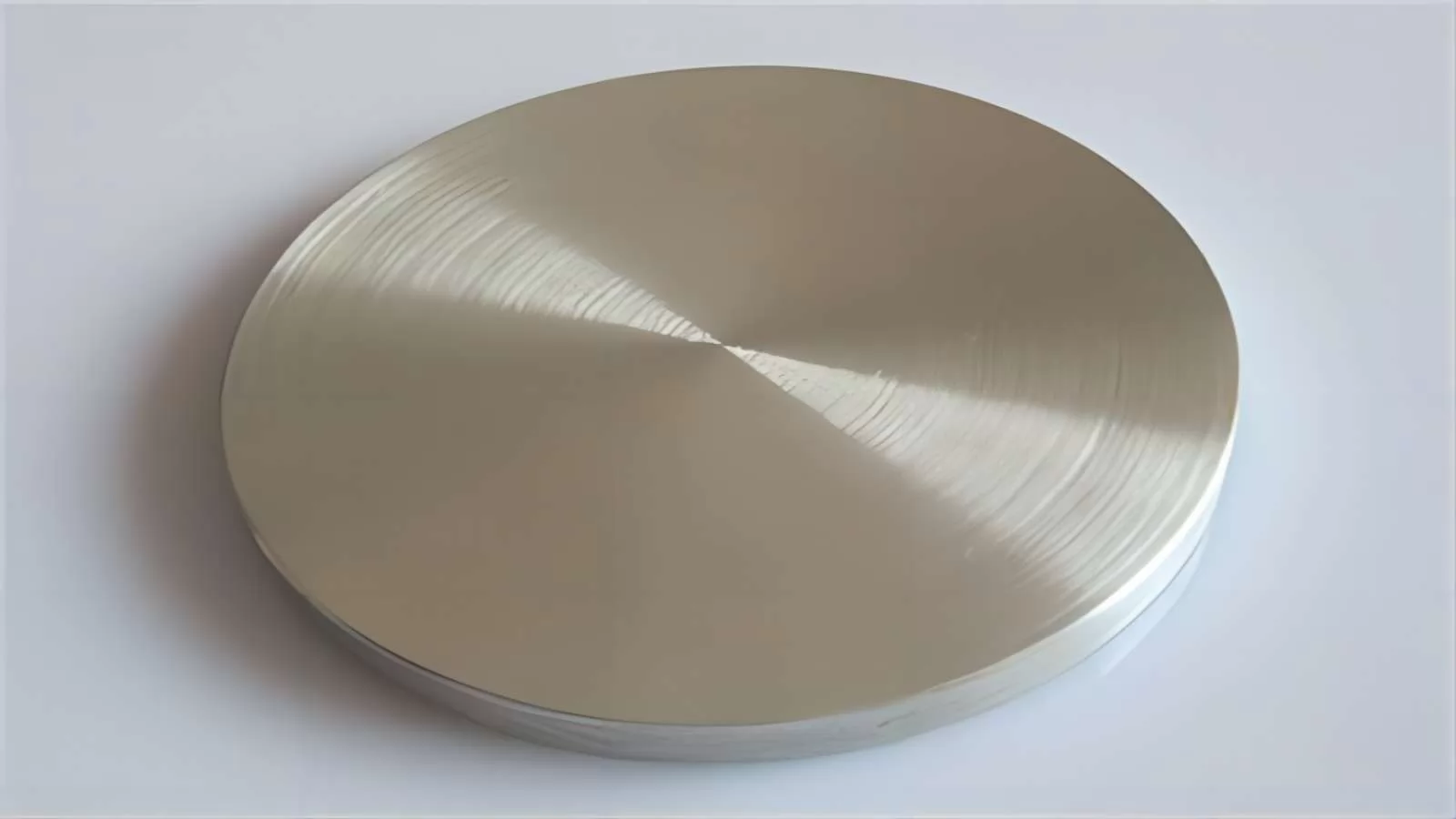
Advantages and Disadvantages of Ferrite Magnets
Advantages:
- Affordability: Ferrite magnets are cheaper to produce than many other types of magnets.
- Stability: They maintain their magnetic properties over a wide range of temperatures and operating conditions.
- Resistance: They are resistant to demagnetization and corrosion, enhancing their longevity in various environments.
Limitations:
- Magnetic Strength: Ferrite magnets are not as strong as rare-earth magnets like neodymium.
- Brittleness: They are hard and brittle, making them susceptible to cracking under mechanical stress.
- Size and Weight: For applications requiring high magnetic strength, ferrite magnets tend to be larger and heavier compared to neodymium magnets.
Conclusion
Ferrite magnets are versatile and economical magnets suitable for a variety of applications due to their moderate magnetic strength, excellent temperature and corrosion resistance, and cost-effectiveness. While they may not offer the same magnetic strength as neodymium magnets, their durability and stability make them a reliable choice for many industrial and commercial uses. When selecting magnets for your project, considering ferrite magnets can provide a balance of performance and affordability, especially in environments where high strength is not the primary requirement.
If you need a reliable manufacturer, then it is recommended to contact ketai ,ketai is a new high-tech enterprise specializing in R&D, production, processing and sales of NdFeB permanent magnet materials